Important Factors When Selecting A Cutting Tool
18.05.2023.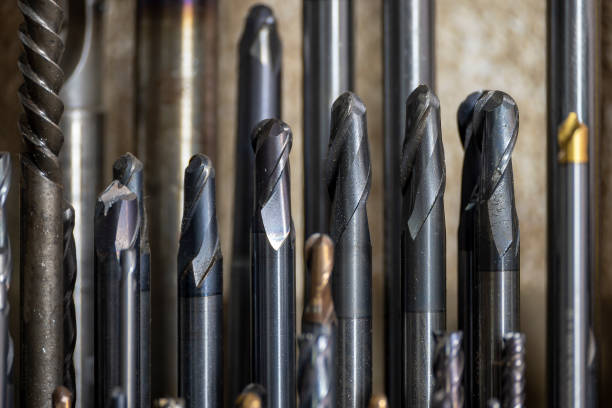
When choosing a cutting tool be sure to take into consideration the material's properties as well as the way it cuts the material. We will discuss the K-factor as well as chemical stability and the cutting angles of the sides, among other things.
The best results can be achieved when you use the correct tool, such as an angle grinder or straight one. Here are a few essential aspects to think about before selecting a tool. Talk to your machine shop about specific equipment if you're not sure what you require. Browse around here to find out an article source on cnc bits for wood.
1. Material Property
The properties of the material used in cutting tools are the basic prerequisites for the success of machining operations. Unlike knives, these tools need to be able to endure high temperatures, without losing their cutting edge. They also have to resist abrasion and adhesion, and are thermally conductive.
These factors are crucial for the optimum performance of cutting instruments. We will examine the material properties of cutting tools in order to comprehend their use and longevity.
Production is contingent on the cutting tool's lifespan and the speed at which it operates. Cutting tool life depends on several factors, including feed rate, tool geometry, and tool wear. The factors mentioned above will affect tool life and increase productivity.
The lifespan of a quality machine is measured by hundreds of thousands, or even more of cutting operations. The life of the tool is determined by the ability of cutting different material at various speeds. Tools for cutting must last and be sturdy, as well as have fast cutting speeds. It is crucial to be aware of cutting speed as well as feeding rates prior to buying a tool.
2. K Factor
K-factor of the cutting tool determines the appearance of the edges. The radius of the cutting edge is contingent on a number of variables, such as the type of material, machine technique and the type of layer.
The most common method of evaluation is with cutting speeds of around 35 m/s. Fig. shows the monitoring area at an edge on the cutter. 1. The size of both the Sa and Sy can affect the force and heat loads.
A tool made from metal Alumina, abrasive and metal is used to measure the K-factor for cutting equipment. Its K factor is influenced by the length of the contact as well as the angle g. The more the rake angle g increases, the objective roughness function also increases.
The more complex the material, the more complex the objective roughness function. A higher K factor means the tool for cutting isn't operating properly.
3. Chemical Stability
CBN-based cutting tools are made from a specialized material. They also resist high temperatures and have outstanding thermal stability. They're typically described as low or high-c-BN. A low-cBN model has no CBN and the high-cBN ones contain between 75 and 95 volume% boron-nitride, along with metallic binder.
Although greasy oil is the most common cutting fluid, the other characteristics are not outstanding. In addition, they are high-cost and generate substantial smoke that is not ideal for modern production. But, they are able to be made low-viscosity when they are mixed along with EP additives. A combination of mineral oils and EP additives provides good seal and extended tool's life.
4. Side Cutting Edge Angle
Back rake angles define the angle of a cutting edge. It's the angle between the tool's surface and a perpendicular plane, measured from its base. In the event that it slopes downward, the tip is positive, while if it is upwards, the angle will be negative.
The typical back rake angle is between 5 and 15 degrees. It's crucial to be aware of the angle you will need when creating or designing the instrument.
The rake of a tool for cutting is determined by the angle formed between the surface of the device as well as the line that runs parallel to the base of the tool. This angle helps reduce friction between the tools and the workpiece. This can result in a thinner and better chips.
However, positive rake angles reduce the strength of the cutting edge segment and decrease the heat conduction capability of the tool. A positive rake angle is more suitable for alloys made of tough metals. Negative rake angle is preferred for soft or weak material.
5. The High Yield At Operating Temperature
High yield strength is one of the most popular features that is present in HSS tools. But, with this kind of tool, the tool edge is loaded close to the limit of its yield strength, leading to severe adhesive wear.
Cutting with materials that are chemically tough will result in increased wear. In addition to severe wear to adhesives, HSS cutting tools are additionally prone to blunting the edges of their blades due to the excessive friction. This article explains the causes which affect the yield of cutting equipment.
A tool's operating temperature is a primary factor determining how much heat is generated by the tool when cutting. If the cutting speed is increased, the maximum temperature of a tool will increase. It is due to the fact that the heat that flows into the tool can affect the material's temperature.
The impact of this is most noticeable with the cutting process that is intermittent. The operating temperature plays a crucial role in determining the longevity of the tool as well as its quality. To extend the lifespan of tools and decrease heat generated it is necessary for the tool to operate at a specific temperature.
6. Tools
Tool hardness is a measure of the capacity of a material's materials to resist the heat, prevent plastic deformation and retain toughness even at very high temperatures. Also, it affects the wear resistance.
The more stable thermally an item is, the greater its ability to withstand the cutting process. Its temperature will be reduced during cutting, if it is equipped with a better thermal conductivity. Selecting a material that is able to endure high-speed cutting is also important.
In the industrial sector The quality of the cutting tools is essential. It affects the amount of material to be removed, its final surface finish, the tolerance, and the cost for the maker.
The Last Said Words
When selecting the best tools and materials, the manufacturer can cut down on scrap, improve production and improve part quality. This can ensure the effectiveness of their operations for a long time. To select the ideal tool material to use to use for cutting, the manufacturer should first establish the specific requirements.
komentiraj (0) * ispiši * #